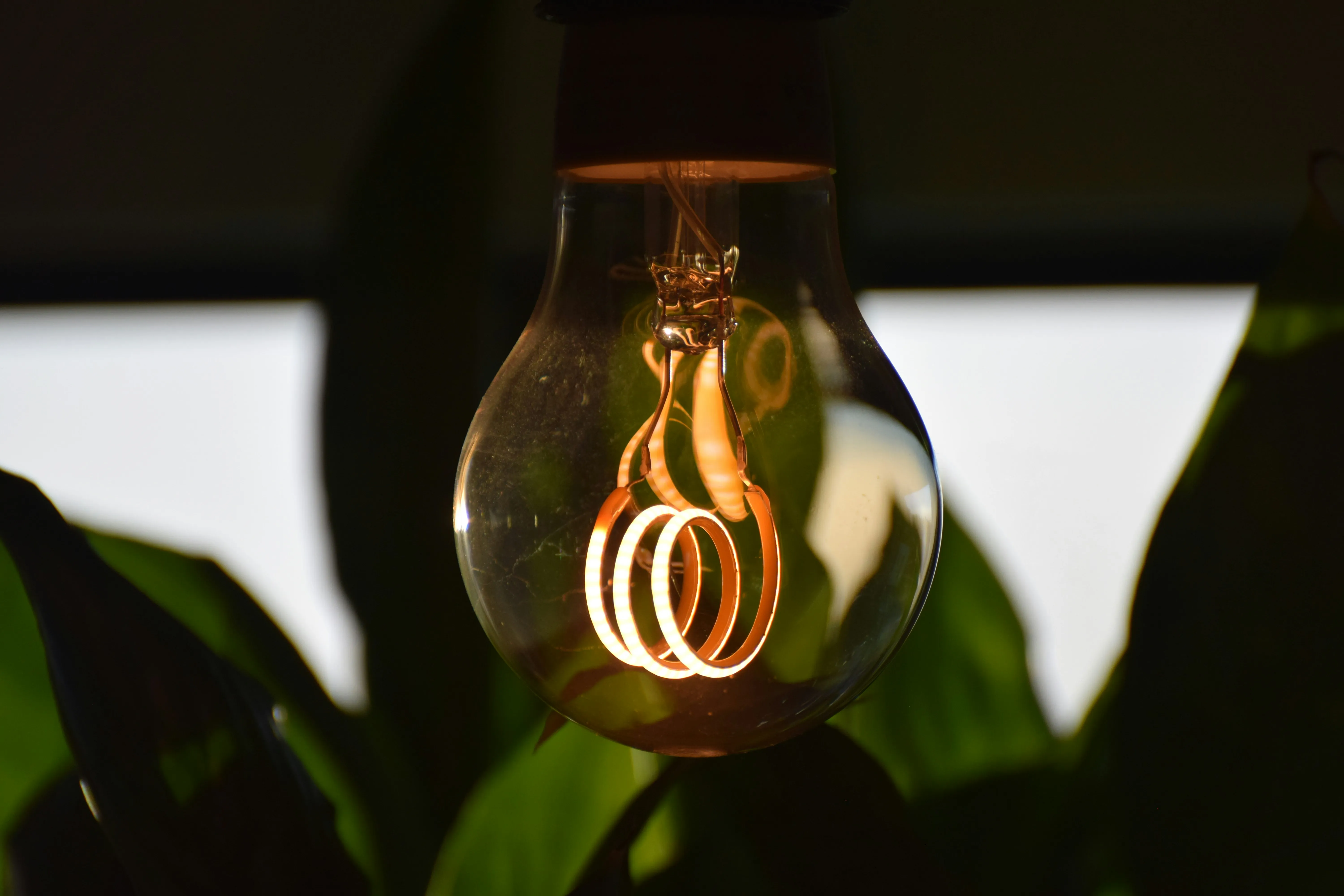
In today's fast-paced business environment, managing a product from conception to retirement is crucial for success. This is where Product Lifecycle Management (PLM) comes into play. Let's explore this essential business strategy and its impact on modern enterprises.
What is Product Lifecycle Management?
Product Lifecycle Management (PLM) is the process of managing a product's entire lifecycle, from its initial concept through design, production, distribution, use, and eventual disposal or recycling. It integrates people, data, processes, and business systems to provide a central hub for all product-related information.
Imagine designing a new smartphone. From brainstorming features to engineering prototypes, manufacturing components, marketing the product, and eventually phasing it out for newer models, the PLM system ensures that every step is well-coordinated and aligned with business goals.
Why companies need a PLM system?
Bringing a product to market is complex, and without the right tools, misalignment, delays, and costly errors are inevitable. Product Lifecycle Management (PLM) software connects every stage - design, development, production, and recycling - into a single, streamlined workflow.
By centralizing data, PLM system keeps teams aligned, reduces errors, and improves decision-making with real-time insights. A study by Tech-Clarity found that companies using PLM solutions experience up to 30% faster product launches and a 40% reduction in development costs, highlighting its role in driving efficiency and profitability.
In a competitive market, agility is essential. PLM software helps businesses cut costs, enhance sustainability, and adapt quickly to change - driving innovation and long-term success.
How Does a PLM System Work?
A PLM system is the foundation of product management, bringing all stages of the product lifecycle into one platform. It centralizes product data, automates workflows, and improves collaboration, keeping everything aligned with business goals.
For example, if an engineer updates a design file, the system instantly notifies the right team members for review. This real-time communication helps reduce errors and speed up development.
PLM software also provides analytics tools that track performance, from production efficiency to customer feedback. These insights enable businesses to make smarter, data-driven decisions to improve products and operations.
Key Stages of Product Lifecycle Management
To fully understand how PLM systems work in practice, let’s break down its three main stages:
1. Beginning of Life
This stage covers everything from ideation to production. It includes activities like brainstorming concepts, designing prototypes, testing materials, and manufacturing the final product.
2. Middle of Life
Once the product is launched into the market, this phase focuses on its distribution, usage by customers, maintenance needs (if applicable), and ongoing improvements based on feedback.
3. End of Life
Eventually, every product reaches the end of its lifecycle. Companies must determine whether to phase it out, recycle components, or introduce a sustainable redesign using PLM software to manage these transitions effectively.
Five Benefits of Using PLM Software
Implementing Product Lifecycle Management (PLM) software can streamline how businesses manage products, improving efficiency, quality, and innovation. Here are five key benefits explained simply:
Ensuring Compliance with Regulations
Regulations can be complex, but PLM simplifies compliance by tracking requirements early and keeping a clear audit trail, helping companies avoid fines and recalls.
Research shows that businesses using PLM systems see:
- 27% fewer recalls
- 31% more compliant products.
Faster Problem-Solving
When issues arise, quick action is crucial. PLM software keeps a full record of a product’s lifecycle, making it easier to trace defects. The companies that use PLM solutions can identify the root cause of problems in minutes rather than hours.
Optimizing Resource Management
Wasted time and duplicated efforts slow teams down. PLM software keeps all design and engineering data in one place, so employees spend less time searching for files and more time innovating.
Reports indicate that top companies using PLM:
- Reduce wasted engineering time by 33%
- Speed up time-to-market by 30%
- Lower development costs by up to 40%
Improving Supplier Collaboration
Seamless communication with suppliers prevents delays and enhances product quality. PLM software ensures everyone has real-time access to design changes, reducing miscommunication and strengthening market position.
Enhancing Product Performance
Tracking product performance post-launch is key to continuous improvement. PLM software helps businesses monitor feedback, warranty claims, and performance data, enabling smarter design updates.
Studies show that companies using PLM are:
- 47% more likely to drive innovation;
- More effective at lowering warranty costs and boosting customer satisfaction.
Challenges of Implementing PLM Software
Implementing PLM software can bring significant benefits, but it also comes with challenges. Here are the key obstacles businesses may face:
- Resistance to Change: Employees may resist new systems. Clear training and communication can help ease the transition.
- Integration with ERP Systems: Integrating PLM with ERP systems can be tricky. ERP manages operations, while PLM covers the product lifecycle. The key challenge is making sure data flows smoothly between the two, even though they serve different purposes.
- Data Migration: Moving data from old systems can be tricky. A phased approach and careful planning can help minimize errors.
- Costs: Initial costs, including software and training, can be high. Cloud-based PLM solutions offer flexibility and scalability to make it more affordable.
With the right strategy, businesses can overcome these challenges and fully leverage PLM software to its full potential.
Differences between PLM and ERP
As mentioned earlier, integrating PLM with ERP systems can be tricky, as each serves different roles. To better understand how they complement each other, here’s a quick comparison:
.webp)
Understanding these differences helps businesses plan how to integrate both systems effectively. PLM and ERP integration is key to connecting product development with business operations.
LoopOS seamlessly integrates with PLM systems, helping businesses manage event credentials and ensure smooth data flow. This boosts efficiency, improves decision-making, and speeds up product development.
For more insights about ERP systems, read the article “Why Traditional ERPs Don't Work for the Circular Economy.”
Future of PLM Technology in Industry 4.0
As product development evolves, PLM software is crucial for enhancing efficiency, collaboration, and innovation, with future advancements further connecting data, processes, and teams.
How AI and IoT are Transforming PLM
- AI-Powered Insights: AI analyzes product data to predict issues and improve product quality before problems arise.
- IoT-Driven Optimization: IoT tracks real-time product performance, allowing businesses to fix problems before they occur, increasing reliability.
- Cloud-Based Flexibility: Cloud PLM enables easier collaboration across teams and helps businesses scale quickly.
- Digital Twins: Digital twins create virtual models of products, allowing companies to test and optimize designs without prototypes.
Unlocking PLM’s Full Potential
As businesses evolve, so does PLM, adapting to new challenges and technologies. Companies that embrace a flexible, data-driven approach will not only streamline operations but also drive innovation and long-term success. PLM isn’t just about managing products - it’s about transforming the way businesses create, refine, and sustain them.
For a deeper understanding of PLM in Industry 4.0, read the scientific article "Challenges and Opportunities in Product Life Cycle Management in the Era of Industry 4.0."