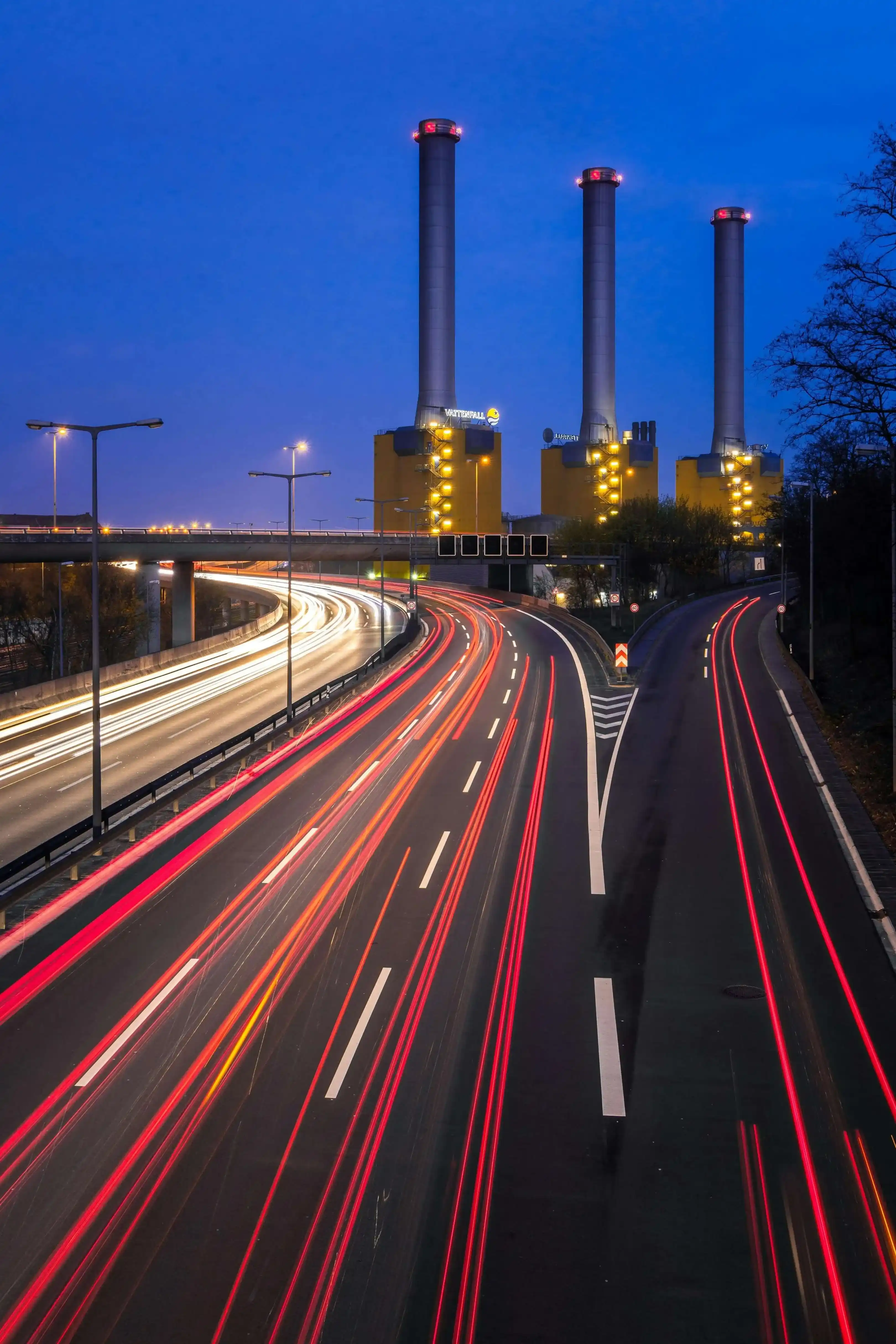
When it comes to digital systems for industrial operations, many companies struggle to understand the differences between ERP, PLM, and MES. These three platforms often overlap, but each plays a distinct role in enabling smarter, more sustainable manufacturing. As businesses aim to align with Industry 4.0 principles and transition toward a circular economy, understanding how ERP, PLM, and MES work, individually and together, becomes essential. This article explores their key differences and helps product-based industries identify which system can best support their goals for innovation, efficiency, and compliance.
What Is an ERP (Enterprise Resource Planning)?
An Enterprise Resource Planning (ERP) is a business management system designed to handle processes like finance, procurement, HR, and logistics. These enterprise systems help centralize transactional data and streamline business workflows, providing greater control and visibility.
Key features of ERP systems:
- Inventory and order management
- Financial planning and accounting
- Procurement and vendor management
- HR and payroll management
- Supply chain coordination
ERP systems are especially valuable for improving data accuracy and reducing administrative overhead across manufacturing and supply chains, as highlighted in insights from the World Economic Forum’s digital transformation reports.
What Is a MES (Manufacturing Execution System)?
A Manufacturing Execution System (MES) manages and monitors shop floor operations in real-time. It bridges the gap between enterprise systems and physical production processes, enabling efficiency and performance tracking.
Key features of MES systems:
- Real-time production monitoring
- Quality control and compliance tracking
- Performance metrics (OEE, downtime)
- Scheduling and resource allocation
MES is critical for manufacturers aiming to adopt smart factory and Industry 4.0 practices, as explored in some studies. When integrated with ERP and PLM, MES becomes part of a robust manufacturing software system.
What Is a PLM (Product Lifecycle Management)?
A Product Lifecycle Management (PLM) system manages all product-related data from concept to end-of-life. PLM plays a crucial role in sustainable product development by ensuring full traceability, supporting circular economy strategies, and integrating Digital Product Passports (DPPs).
Key features of PLM systems:
- Product design and version control
- Cross-functional collaboration (engineering, R&D, quality)
- Specifications and BoM (Bill of Materials) management
- Regulatory and sustainability documentation
- Integration with DPPs and traceability tools
According to research from the European Commission’s Horizon 2020 projects, PLM solutions help reduce time-to-market and enhance product design quality.
To explore how PLM supports digital product compliance and circular manufacturing, check the article: Why Digital Product Passports Are Essential for the Circular Economy
ERP vs PLM vs MES: A Side-by-Side Comparison
.webp)
How ERP, PLM, and MES Work Together in Industry 4.0 and the Circular Economy?
Although they may seem to overlap, ERP, PLM, and MES are complementary systems. Each supports a different layer of the product journey:
- PLM comes first, managing the product concept, specs, and design.
- MES takes over during production, ensuring everything is made correctly and efficiently.
- ERP manages the overall business flow, like procurement, delivery, and finance.
When connected, these platforms create a digital thread—a continuous data flow that links every stage of a product’s lifecycle. As McKinsey notes, building this digital continuity is essential for resilience and innovation.
When Is PLM the Right First Step for Digital Transformation and Product Compliance?
For companies developing complex products, handling compliance data, or preparing for the future of circular manufacturing, PLM can provide the foundational layer needed to succeed.
PLM is especially relevant when:
- Managing multiple product versions and ensuring full revision history
- Facilitating collaboration across departments and suppliers
- Prioritizing sustainability goals and DPP compliance
- Scaling operations and needing centralized control over product data
Solutions like LoopOS are built to support this approach, enabling product-based businesses to structure and control their data while preparing for EU regulatory shifts.
Why Digital Integration Matters
Companies investing in connected enterprise systems—combining ERP, PLM, and MES—gain better decision-making, real-time insights, and greater operational efficiency. This is especially important as manufacturers move toward digital transformation and circular economy goals.
According to the Ellen MacArthur Foundation, digital tools are enablers of circular economy business models, especially in sectors like textiles, electronics, and machinery.
ERP, PLM & MES: Which System Is Right for Your Digital and Circular Strategy?
ERP, PLM, and MES systems each bring unique strengths to modern manufacturing environments. For businesses aiming to innovate, ensure compliance, and drive sustainable growth, understanding these tools is essential.
While ERP supports business operations and MES oversees production, PLM offers visibility across the full product lifecycle—making it a powerful starting point for transformation.
For those seeking to improve product traceability, meet future regulations, or enable circular business models, investing in PLM is a forward-looking move.
For more insights on PLM and sustainable innovation, explore this related blog post: Digital Product Passports and Circular Manufacturing